A friend of mine who tinkers with vintage car parts once wondered aloud: if strong degreaser can strip engine grease in seconds, would it turbocharge an ultrasonic cleaner? It’s a tempting thought—combine mechanical cavitation with solvent power and you’ve got a “super-cleaner,” right? But real-life cleaning is never that simple. What’s safe for a brush bucket isn’t always safe inside a precision machine humming with ultrasonic waves.
So yes, you can use degreaser—but only under carefully controlled conditions and with full awareness of the risks involved. Skip this caution, and you might end up with a tank filled with foam, damaged gaskets, or even a health hazard.
Let’s explore what happens when degreaser meets ultrasound, why it can both help and hurt, and how to apply it the right way—if you choose to go that path.
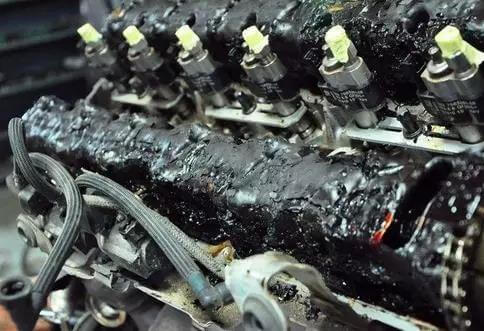
How Ultrasonic Cleaners Work
Ultrasonic cleaning isn’t magic—it’s the power of millions of tiny, collapsing bubbles. A transducer drops an ultrasonic wave (typically 25–45 kHz) into a liquid. This wave forms minuscule cavitation bubbles that implode on surfaces, dislodging grime from cracks and crevices that normal scrubbing can’t reach. But to be effective, the liquid must allow both sound transmission and bubble collapse. Too much foam, or poor chemistry, and you lose efficiency fast.
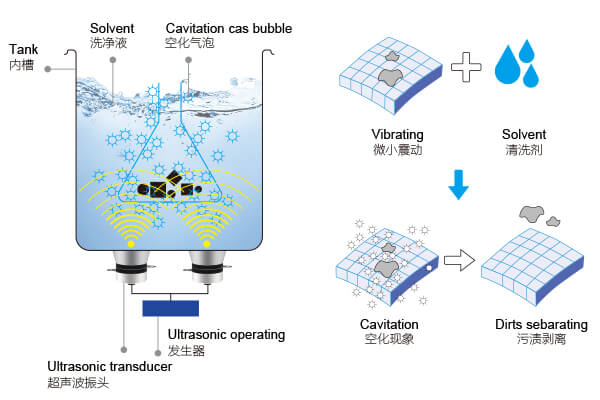
What Degreasers Are and How They Work
Degreasers—whether solvent-based, water-based, or alkaline—are formulated to break down heavy oils and grease. Solvent-based degreasers dissolve fats and hydrocarbons, alkaline blends use saponification, and water-based solutions rely on surfactants and boosters. You see them in garages and industrial workshops for heavy-duty cleaning—but combining them with ultrasonic machines isn’t straightforward.
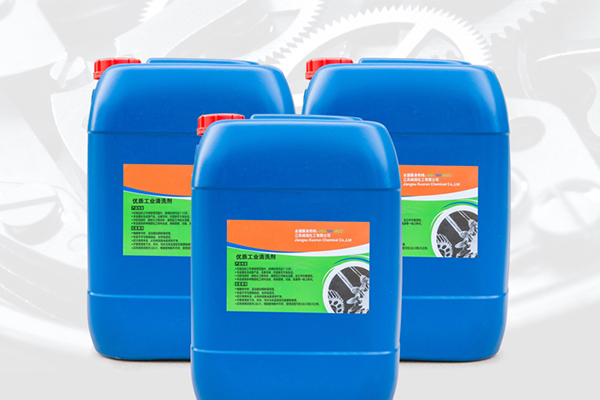
Can You Use Degreaser in an Ultrasonic Tank?
Yes—but only with caution. Degreasers can enhance oil removal when used properly—some formulas improve cavitation and chemical penetration. But they can also:
- Overfoam, killing ultrasonic effect;
- Corrode aluminum or thin stainless steel, damage seals and electronics;
- Release VOCs, which can be toxic or flammable;
- Introduce fire/explosion risk, especially under heat.
So unless you’re using low-foam, ultrasonically tested degreasers, you’re walking a safety tightrope.
Enhanced Oil Removal vs Overfoaming
A degreaser-infused ultrasonic cycle can clear engine grease or stains in half the time. But if foam takes over, the cavitation collapses, and your cleaning power crashes—with the added bonus of a microwave-like disaster of foam overflowing onto your bench or floor.
Professional labs often use diluted degreaser in combination with ultrasound, but only under strictly controlled dilution (10:1 to 50:1), and they monitor foam aggressively.
Potential Risks
- Corrosion: Strong solvents can weaken metal tanks or seals designed for water-based detergents.
- Seal/Gasket damage: Organic solvents may dissolve silicone or rubber parts.
- Health hazards: Many degreasers emit VOCs—harmful to breathe and possibly flammable.
- Warranty void: Using improper cleansers often voids equipment warranties.
Best Practices for Safe Usage
If you decide to experiment:
- Always check manufacturer’s guidelines—some ultrasonic tanks are rated for solvent use.
- Stick to low-foam, ultrasonic-compatible formulas with clear safety data (SDS).
- Dilute heavily: start at 20:1 and never exceed 10% degreaser.
- Maintain water temperature of 40–55 °C to balance cleaning potency with safety.
- Ventilate the workspace thoroughly.
- Test on scrap metal first to ensure compatibility.
Research-Based Insi
ghts
Ultrasonic cleaning relies heavily on the properties of the cleaning solution to optimize cavitation and soil removal. Several studies outline how solvent-based or alkaline blends perform compared to traditional detergents or plain water:
- According to Ultrasonics Cleaning (Wikipedia source), ultrasonic cleaners often use water-based detergents or hydrocarbon solvents specifically to dissolve oils and greases. Surface tension reduction by surfactants notably enhances cavitation efficiency and contaminant removal (Links:https://en.wikipedia.org/wiki/Ultrasonic_cleaning).
- A review in Ultrasonics Sonochemistry highlights that aqueous alkaline solutions (commonly used as degreasing agents) effectively remove oil and grime from machinery parts when combined with ultrasonic agitation. These low-foam alkaline blends support robust bubble formation without equipment compromise (Links:https://www.sciencedirect.com/science/article/abs/pii/S1350417708001533).
- Industrial systems sometimes integrate vapor degreasing, combining organic solvents with ultrasonic cleaning for hard-to-remove contaminants. These are designed to reuse solvents safely and minimize component wear (Links:https://en.wikipedia.org/wiki/Ultrasonic_cleaning).
However, other studies caution against prolonged ultrasonic exposure with harsh chemicals:
- Research on ultrasound during acid etching in metal treatment found that extended ultrasonic cavitation, especially in aggressive chemical solutions, can accelerate corrosion or etching of anodized layers (Links: https://en.wikipedia.org/wiki/Ultrasonic_cleaning , https://www.sciencedirect.com/science/article/pii/S1350417718314706).
What This Tells Us
- Solvent-based or alkaline degreasers can significantly enhance ultrasonic cleaning performance for oily or greasy parts—if low-foam, properly formulated, and used with caution.
- Such blends should be NSF or ASTM/ISO compliant, and manufacturers often integrate vapor degreasing for heavy diesel parts (Links:https://crest-ultrasonics.com/solvent-ultrasonic-cleaning-systems/).
- Aggressive solvents or prolonged cycles can damage anodized or coated surfaces—especially if tank heating or chemistry isn’t controlled (Links:https://www.sciencedirect.com/science/article/pii/S1350417718314706 , https://www.mdpi.com/journal/materials/special_issues/Anodizing_Metals).
These authoritative sources support a balanced approach: degreasers can work well within a controlled framework, but improper use risks equipment integrity and safety.
Real‑World User Experiences
Turning to the real world, many mechanics and hobbyists share their firsthand experiences online—with a common theme: degreasers can be effective in ultrasonic applications, but they come with trade-offs.
On r/smallengines, a user shared:
“I’ve had really great luck with Simple Green but it ends up with me having to drive 2 hours into the city to get it. … I’ve also used purple style degreaser but I’ve heard it can do harm to carbs if submerged for more than 30 minutes.” ( Links:https://www.reddit.com/r/smallengines/comments/mejj2k/what_do_chemical_degreaser_do_you_use_in_your/)
That experience highlights both the performance benefit and material risks of overuse.
Meanwhile, on r/BikeMechanics, another enthusiast offered a workaround by bagging parts:
“I stick items like the chain, cassette etc. in a Ziploc bag with citrus degreaser then dunk it in the bath filled with water. They come out like new.” (Related Links:https://www.reddit.com/r/BikeMechanics/comments/t3w2bn/what_fluids_are_you_using_in_your_ultrasonic/)
This method mitigates direct contact between the solvent and the tank, reducing damage to seals and materials.
What This Reveals
- Degreasers like Simple Green are effective, but using them undiluted or for extended times can harm sensitive parts.
- Bagging or containing degreaser minimizes risk to the cleaner’s internal components.
- Real users echo the message from studies: ultrasound plus chemistry is powerful—but context and method matter.
Alternatives That Work Without Solvents
If degreaser seems too risky:
- Use enzyme or alkaline detergents rated for ultrasonic cleaning.
- Consider emulsifying agents specially designed to lift grease.
- Use a two-step cleaning: first degreaser soak manually, then ultrasonic rinse with water-based detergent.
These options keep performance high without compromising equipment or safety.
Maintenance After Degreaser Use
After any degreaser run:
- Run clean water cycles until foaming stops.
- Wipe the tank carefully to remove solvent traces.
- Inspect and clean seals, lubrication points, electronics.
- Dispose solvent waste as required by local hazardous material guidelines.
Final Considerations Before You Try It
Relying on degreaser in your ultrasonic cleaner comes with risks—and potential rewards. If you’re cleaning heavy oil-laden mechanical parts and are ready to commit to safety and maintenance, it’s possible to boost performance. But for delicate tools, electronics, or general use, a proper ultrasonic or enzyme cleaner is both safer and more reliable.
Let your cleaning mission guide the method—not just the excitement of combining ultrasound and solvent.
FAQs
1. Will degreaser void my ultrasonic cleaner warranty?
Often yes—check your manual; many manufacturers prohibit solvent use.
2. How much degreaser should I add?
Keep it low—typically 1–5% by volume, and always follow the product’s SDS guidance.
3. Can I use any automotive degreaser?
No. Only choose low-foam formulas certified for ultrasonic use.
4. What about degreaser vapors?
Ensure good ventilation and consider using a fume hood or external vent.
5. Is a degreaser mix better than enzyme cleaners?
For heavy oil, yes—with tradeoffs. Enzyme formulas are safer and adequate for many use-cases.
6. How often should I change degreaser solution?
After every heavy load or when contamination level is high—usually after one full cycle.