Compressor parts and components due to stamping, machining and the generation of pollutants for dust, cutting oil, coolant, oil, metal chips and other dirt, need to be cleaned.
Ultrasonic cleaning equipment capacity
Compressor parts size range of 110 × 40mm minimum, maximum 190 × 210mm. according to the annual cleaning capacity of 400,000 sets, annual working days 250 d calculation, four cleaning machines, working 8 h per day, the daily output of 1600 sets.
Ultrasonic cleaning fluid selection
The original cleaning agent is CFC-113, now is an alternative solvent HEP-2, its main component is n-bromopropane (nPB), performance and CFC-113 and TCA almost exactly the same, better wetting coefficient, stronger cleaning ability of metal parts. It has no flash point, can be recycled again and again, and has very low operating cost. The cleaning process is the same as CFC-113, no need to update the equipment, and the steaming temperature can be increased appropriately. The bromine cleaning solution is friendly to, ODP value is 0.006, lifetime in the atmosphere is 11 d, almost no GWP value. The U.S. EPA said in March 2002: accept nPB as a solvent for cleaning, aerosols and adhesives, but the use should be controlled in the air exposure concentration.
Ultrasonic cleaning equipment structure composition and operation description
The cleaning equipment is composed of four tanks, which are two cleaning tanks, one steam bath washing tank and one distillation recovery tank, equipped with ultrasonic no generator, circulating filtration system, automatic temperature-controlled heating system, freezing system, as well as inlet and outlet conveying rollers, manipulator ﹑ control panel, fully enclosed outer cover and electric control system, etc.
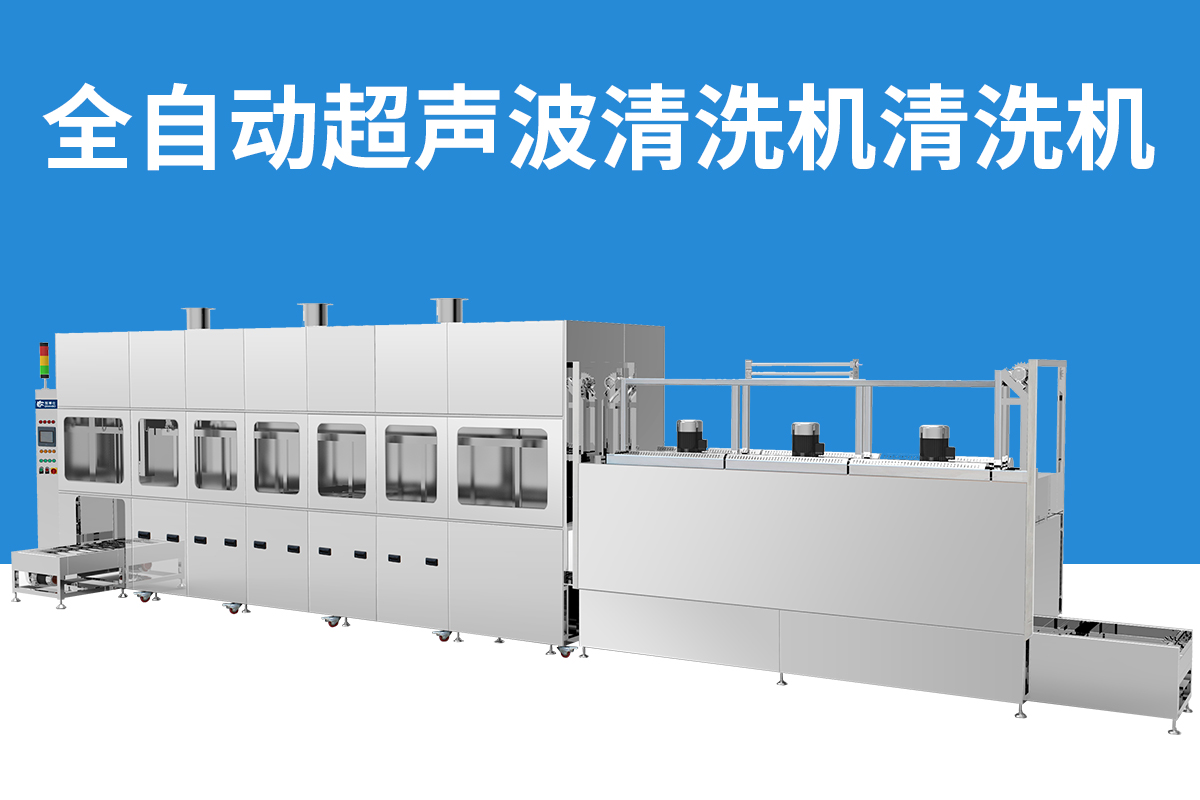
The cleaning machine is fully automatic equipment, the cleaning process is controlled by the program. After the operator starts “automatic operation”, the cleaning basket with the workpiece will be placed on the inlet and outlet table, and the material sensor will sense the cleaning basket, which will be sent to the first rough washing tank by the conveyor roller. The single-arm robot will lift the cleaning basket at this place and send it into the ultrasonic rough washing tank, rough washing, fine washing, spraying or steam rinsing, cooling and drying according to the established process sequence, after the workpiece is cleaned, it will be sent back to the receiving table by the robot and conveying roller conveyor, and a signal will be sent out for discharging, the operator will unload the cleaning basket at the same place and replace the workpiece to be washed and start to repeat the automatic cleaning procedure. The whole washing machine is fully enclosed outside the opening/closing door at the in/out material table, and the equipment has a transparent observation window at the front of the operator and a removable access door at the back.