Ultrasonic cleaning machine transducer is the energy conversion device. Its main applications are ultrasonic cutting equipment, ultrasonic atomization spraying equipment, ultrasonic metal melt processing equipment, ultrasonic welding equipment, ultrasonic liquid processing acoustic chemical equipment and ultrasonic metal fatigue test equipment. The frequency of the transducer is usually between 20KHz~120KHz.
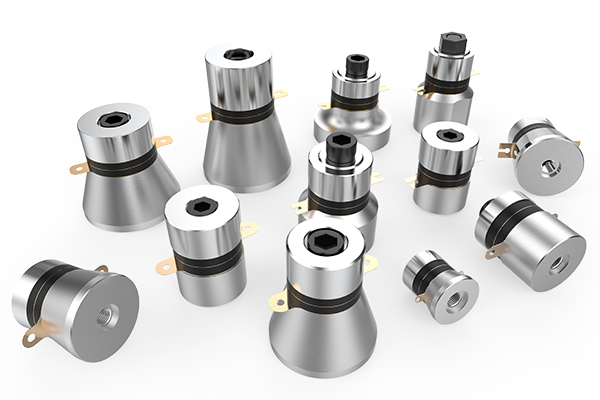
Ultrasonic transducer structure.
Ultrasonic transducer mainly includes shell, acoustic window (matching layer), piezoelectric ceramic disc transducer, backing, lead-in cable, Cymbal array receiver and other major components. The piezoelectric ceramic disc transducer plays the same role as the general transducer, mainly used to transmit and receive ultrasound; and in the piezoelectric ceramic disc transducer above the Cymbal array receiver, mainly by the lead cable, Cymbal transducer, metal rings and rubber gaskets, used as an ultrasonic receiver to accept the Doppler redirection signal generated outside the frequency band of the piezoelectric ceramic disc transducer.
Working principle of ultrasonic transducer.
Ultrasonic transducer, the use of its resonant frequency of the same piezoelectric ceramic piezoelectric effect, the conversion of electrical energy into mechanical vibration. Usually first by the ultrasonic generator to generate ultrasound, by the ultrasonic transducer will be converted into mechanical vibration, and then by the ultrasonic export device, ultrasonic receiving device can produce ultrasound. Therefore, as an energy conversion device, the function of the ultrasonic transducer is to convert the input electrical power into mechanical power (i.e., ultrasound) and then pass out, while its own consumption of a small part of the power.
Ultrasonic transducer structure mainly has a shell, sound window (matching layer), piezoelectric ceramic disc transducer, backing, lead-in cable, receiver and other major components. Among them, the piezoelectric ceramic disc transducer has the same role as most transducers, mainly used to transmit and receive ultrasonic waves; ultrasonic receiver in the piezoelectric ceramic disc transducer above, mainly by the lead cable, transducer, metal ring and rubber gasket, receive the piezoelectric ceramic disc transducer outside the frequency band generated by the Doppler dial signal.
Ultrasonic transducer parameters are detailed.
① resonant frequency: f, unit: KHz
Frequency is the frequency measured by the transmission line method using a frequency generator, millivolt meter, or by a similar instrument such as an impedance characteristics analyzer. It is often referred to as the small signal frequency. The opposite is the frequency of the machine, i.e. the actual operating frequency measured by the customer when the sensor is connected to the drive power supply (with or without load) via a cable. The same transducer with different drive power supplies will display different frequencies because the customer’s matching circuitry is different. Such a frequency cannot be used as an ordering basis.
②Transducer capacitance: CT, unit: PF
That is, the free capacitance of the transducer can usually be measured at 400Hz-1000Hz by a capacitor bridge, or an impedance characteristic analyzer can be used. For the sake of simplicity, measurements using a common portable capacitance meter can also meet the requirements.
③The way the sensor works
Due to the different processing methods and requirements, the working mode of the transducer can be roughly divided into continuous operation (lace machine, CD sleeve machine, zipper machine, metal welding, etc.) and pulsed operation (e.g. plastic welding machines). The different working methods are different. The requirements of the transducer are different. In general, continuous work has almost no pause time, but the working current is not very high, and pulsed work is intermittent, with a pause, but a high instantaneous current. On average, the power in both states is important.
④ Sensor type and maximum power
Machine manufacturers may have different nominal power for different purposes and aims of the machine. In other words, for different machines, the same transducer may have different nominal power. To avoid ambiguity, the customer should specify the type of transducer construction, such as column type, inverted horn type, etc., as well as the diameter and number of piezoelectric ceramic wafers.
⑤ Mounting dimensions
There are mainly horn materials, surface treatment methods and shapes. The diameter, thickness, number and position of notches or screws on the flange of the transducer connected to the horn, the horn connected to the mold.