High pressure system is the advanced fuel system to meet the emission standard of diesel engine III or above, and is the direction of diesel fuel system development. With the increasing working pressure, the geometry and processing precision of the products are also increasing. With the continuous improvement of emission requirements, the aperture of the injector nozzle spray hole is getting smaller and smaller, and the requirement of the flow coefficient of the spray hole is also increasing. Injector nozzle, plunger, valve and other precision parts are the key components of the diesel injection system, its work reliability and service life directly affect the performance of diesel engines. After improving the processing accuracy of the product, reducing the clearance of the fittings, reducing the diameter of the spray hole, the cleanliness of the system has become the outstanding problem that restricts the consistency and stability of the working parameters of the zero part of the high-pressure system.
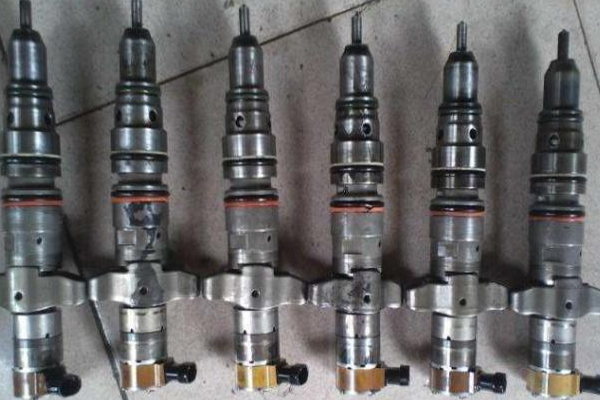
Oil pump, injection nozzle cleaning characteristics
High-pressure system parts are many types, cavity complex, including a large ratio of the length of the return hole, with internal and external threads of the injector, control valve coupling, injection nozzle coupling, etc..
Oil pump, nozzle manufacturing process pollutants are mainly abrasive paste residues, abrasive particles, iron chips, kerosene, diesel oil, quenching oil, mechanical oil, dust, sweat, fingerprints, etc., of which the abrasive paste residues is a strong adhesion of dirt.
Oil pumps, oil nozzles are generally produced in large batches, and are often cleaned on multi-station cleaning machines.
Oil pump, injector cleaning agent selection
Cleaning agent is one of the important factors affecting the cleaning effect, should be based on the oil pump, oil nozzle material structure shape, the nature of dirt and cleanliness requirements to choose.
① Earlier (1990s) cleaning fluid is generally hot diesel and gasoline. Because of high energy consumption, flammable and explosive, manual operation, cleaning quality and efficiency is low, and labor intensity, is now eliminated.
② water-based cleaning fluid + surfactant. Mainly through surfactants, reduce the surface tension of the aqueous solution, with wetting, emulsification, dispersion and solubilization and other physicochemical effects, to achieve the purpose of decontamination, suitable for most of the oil cleaning.
③ solvent cleaning agent, here refers to petroleum monsters, halogenated by, alcohols, ethers, esters have the ability to dissolve oil organic solvents. For example, alternative ODS solvent n-bromopropane (nPB), AK-225, hydrocarbon solvent, etc.
Ultrasonic oil pump, oil injection nozzle cleaning process
Process 1: [water-based soaking + ultrasonic 1] → [water-based soaking ten ultrasonic 2] → [water-based soaking + ultrasonic 3] → [water-based soaking + ultrasonic 4] → [hot DI water rinsing] → [hot DI water spraying] → [wind ten hot air drying] → [immersion antirust oil + hot air drying]
a. The ultrasonic frequency is 28~40kHz selectable, and the power can be adjusted according to the size of the workpiece.
b. The first slot to the fourth slot cleaning solution is water-based + surface activator, electric heater heating 80 ℃, soak ultrasonic removal of abrasive paste and grease dirt.
c. Select DI water rinsing, heating to about 95 ℃, supplemented by mechanical throwing to remove the remaining dirt.
d. Hot DI water spraying, to stop the secondary adsorption of cleaned particles dirt, hot spraying is conducive to water-based evaporation drying.
e. Wind knife + hot air drying is conducive to the removal of residual liquid, with hot air drying must be filtered compressed air, the accuracy of the hot air filter used is 0.1um, hot air temperature is adjusted to 60 ~ 65 ℃ when the hot air drying without any residue.
f. Clean oil pumps, oil nozzles and other components for anti-rust treatment, the product will not produce corrosion and rust, which is an important process for water-based cleaning of precision metal parts.
Process 2: [solvent soaking + ultrasonic 1] → [solvent soaking + ultrasonic 2] → [pure solvent spray] → [vapor phase rinsing] → [condensation drying] → [antirust treatment]
a.The ultrasonic frequency is 28~40kHz selectable, and the power can be adjusted according to the size of the workpiece.
b.The solvent is AK-225 + ultrasonic. The KB value of AK-225 is 31, which means it has balanced solvency power for grease dust and other dirt, and increases ultrasonic cleaning to accelerate dissolving abrasive paste and grease pollutants.
c. Pure solvent spray washing, supplemented by multi-station fixture rotation movement, so that the spray washing workpiece without dead ends, reducing secondary pollution and removing the remaining dirt.
d. Vapor phase rinsing, the latent heat of vaporization is small, indicating that the energy consumption of vapor generation is small and easy to dry.
e. Condensation drying, the workpiece put forward steam area, in the condensation layer for a short time, the oil pump nozzle parts that fully dry, complete the cleaning process.
f. Cleaning equipment can be the same as the original four tanks with solvent recovery and regeneration device, only the cleaning solvent from CFC-113 (ODS substances) can be replaced by AK-225.
g. When using AK-225 for cleaning, in order to reduce solvent leakage, the water supply temperature of the chiller can be reduced or the height of the condensing coil can be increased.